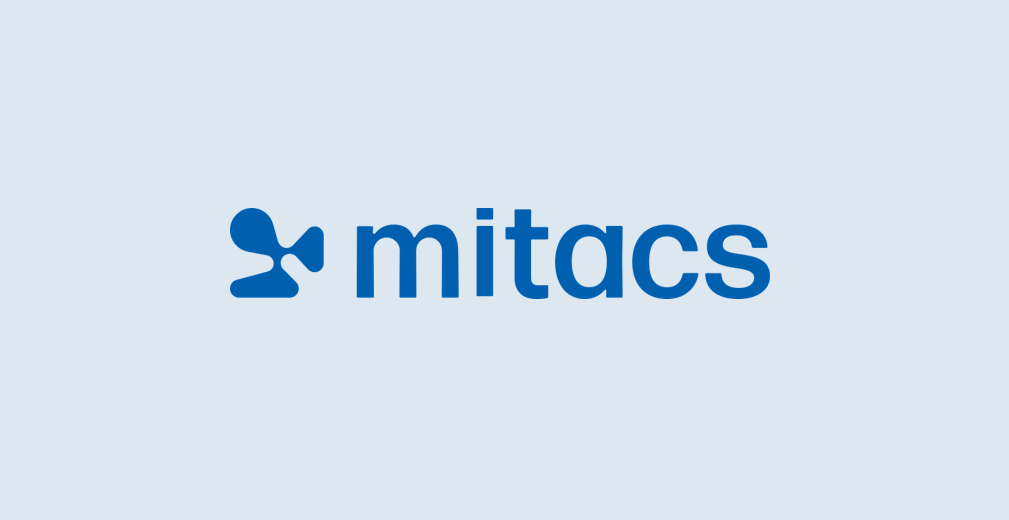
PWC effectue des tests sur les compresseurs lors du développement de ses moteurs afin de mieux connaître les niveaux vibratoires des ailettes en fonctionnement. Le but de ce projet de recherche est de développer une méthode numérique basée sur des considérations aéroélastiques et capable de prédire efficacement ces niveaux vibratoire afin de limiter la voie […]
Read More